Development Story
New Technology Enables Adhesion of Fluoropolymers, Not Possible Until Now
Fluoropolymer materials with unprecedented adhesive properties
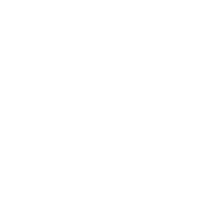
AGC’s fluoropolymer products under the Fluon brand have been deployed in numerous fields, including semiconductor, automotive, energy and construction. On July 1, 2018, AGC launched Fluon+ as a new brand designed to cater to the improved sophistication of industrial technologies, and to the increase in demand for fluoropolymers. The Fluon+ brand is a new range of new fluoropolymers, based on AGC’s fluoropolymer compounding and processing technologies, enhanced with additional functionality added to meet customer requirements.
In particular, the Fluon+ ADHESIVE series is a range of groundbreaking products which offer adhesive and dispersive properties and a level of compatibility with other materials that was not achievable with fluoropolymers (which do not adhere readily to other materials) until now, while at the same time maintaining the excellent heat resistance and electrical properties of existing fluoropolymers.
These properties of Fluon+ ADHESIVE now enable the functionality of fluoropolymers to be added to metals, polymers and other materials by bonding them with Fluon+ ADHESIVE fluoropolymers to create composites. There are now high hopes for the application of Fluon+ ADHESIVE products in numerous fields, including the auto parts and energy industries, as well as in the manufacture of materials for printed circuit boards (PCB) for use in fifth generation (5G) mobile telecommunications systems, which demand low transmission loss and high heat resistance.
Enabling the coexistence of non-stick and readily-adhesive properties
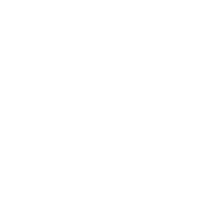
“We were consulted by customers in the automotive industry, who said that, owing to the toughening of environmental regulations, there was a need for them to manufacture fuel hoses with a higher level of barrier performance. They wanted to know whether it was possible to use fluoropolymers. Fluoropolymers have high resistance to gasoline and offer high-level performance as barriers, so they can prevent the permeation of gas from nylon fuel hoses. However, they cannot be bonded with the nylon layer. And so we began the development based on the premise of creating a fluoropolymer with the additional property of adhering readily to other materials. But the (initial) development was a continuous string of failures,” explains development team member Naoko Sumi (Manager, AGC Chemicals Company), regarding the development process.
With the toughening of vehicle emission regulations, there was an urgent need in the automotive industry not only to reduce emissions from engines but also to reduce evaporative emissions permeating through fuel hoses. Fluoropolymers soon became the focus of attention for use as a material for preventing these emissions due to their high-level performance as barriers, their resistance to oils and chemical agents, and their excellent molding characteristics. If a fluoropolymer layer could be applied to the inside of nylon fuel hoses, it would be possible to prevent the permeation of gases.
However, fluoropolymers have conventionally been marketed for their non-adhesive properties, as demonstrated by their use in water repellant materials and non-stick coatings for pans and other cookware. Since fluoropolymers would not adhere to nylon in their existing form, it was not possible to manufacture multilayered nylon/ fluoropolymer hoses. In order to create such hoses, it would be necessary to give fluoropolymers adhesive properties. In other words, there was a need to develop a new type of fluoropolymer, which would maintain the desired original properties, together with the inherently opposite characteristics of not adhering to other materials yet at the same being readily adhesive. This marked the beginning of the challenge to create a new type of material that had not existed before.
Days of repetitive prototyping and evaluation
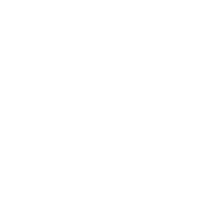
The development process, as Sumi says, was a string of continuous failures. Initially, the developers attempted to impart adhesive properties by devising molding techniques for process-bonding the fluoropolymers to the hoses. However, they were unable to achieve high level adhesive properties in this way. Next, they returned to the drawing board and reviewed the polymerization process used to create the basic polymer raw material. Sumi—who was responsible for polymer development—used substances that would contribute to adhesive properties, and spent days repeating the polymerization process while continuously changing the composition. The newly created fluoropolymers were passed to the evaluation team, who conducted property testing and tested for adhesion with other materials. Time and time again, the evaluations produced the same result: no adhesive properties.
Despite these setbacks, the polymer development personnel continued to alternate and perform polymerizations every day. Although occasionally there were clashes of opinion with regard to experimental methods and the direction that the development was taking, the development gradually approached completion.
Full team meetings were held almost every week, and even sales division personnel began to come involved in the development in addition to R&D personnel. AGC proceeded with the development as a united team, heading towards its goal of creating a new type of polymer: a fluoropolymer with adhesive properties.
Eventually, after a seemingly endless process of repetitive prototyping and evaluation, the team arrived at a composition that worked, and could finally see their way to meet the adhesive requirement. But then a new issue emerged. Automobile fuel hoses also require electrical conductivity to eliminate the static electricity that arises when gasoline flows through the hose at high speed. The team continued to produce many more prototypes, and eventually succeeded in creating a new adhesive fluoropolymer product with this new additional feature. This marked the birth of a polymer with inherently opposed characteristics: resisting adhesion to other materials yet also being capable of adhesive bonding.
“One aspect of the development was that the entire company came together and cooperated on this single massive project, to resolve this problem for the automotive industry. Although there were many obstacles to overcome in this development, I think that the commitment and determination of all the team members to answer to the expectations of customers was a major point in enabling us to arrive at the successful completion of this project,” says Sumi.
Growing technological capabilities to cater to customer expectations
The adoption and use of Fluon+ products created by the development team is progressing not only in the automotive industry, but also in a diverse range of other fields, including telecommunications, energy and construction.
For example, the creation of 5G telecommunications systems—which facilitate high-speed high-volume communications—requires the use of higher precision PCBs, and there was a need to combat issues such as transmission loss and heat generated by circuitry.
Although fluoropolymer materials—with their low electrical permittivity and low dielectric dissipation factor—were capable of fulfilling these requirements, there were also significant hurdles to their adoption since conventionally it was not possible to bond them with the metallic components used in electronic circuitry. Fluon+ ADHESIVE is an ideal material for PCBs because it bonds easily with metals, and is readily compatible with other materials. In the future, we expect to see a major increase in demand in this field.
The Fluon+ range will also continue to evolve, as we develop products with higher level adhesive properties, while incorporating the needs of customers. There is no doubt that AGC’s Fluon+ will continue to be one possible solution for catering to increasingly higher requirements for materials in various fields. When customers wish to add the properties of fluoropolymers—such as resistance to heat and chemical agents, electrical properties, water repellency and lubricity—to their existing materials, AGC’s Fluon+ will offer an ideal solution.
Moreover, AGC continues to produce a constant stream of other new products that cater to customer needs. The evolution of AGC’s technologies is a result of relentless refinement to live up to the expectations of customers. “Isn’t there a material with these properties?” “Is it possible to use this material to do this?” Even the smallest request is fuel for our development efforts.
We would love to hear from you about your problems. Until now, AGC has accumulated skills and experience through its involvement with manufacturing workplaces and product in a diverse range of fields. We solve problems using the world’s latest cutting-edge technology. Please consult us regarding any issues you may have.